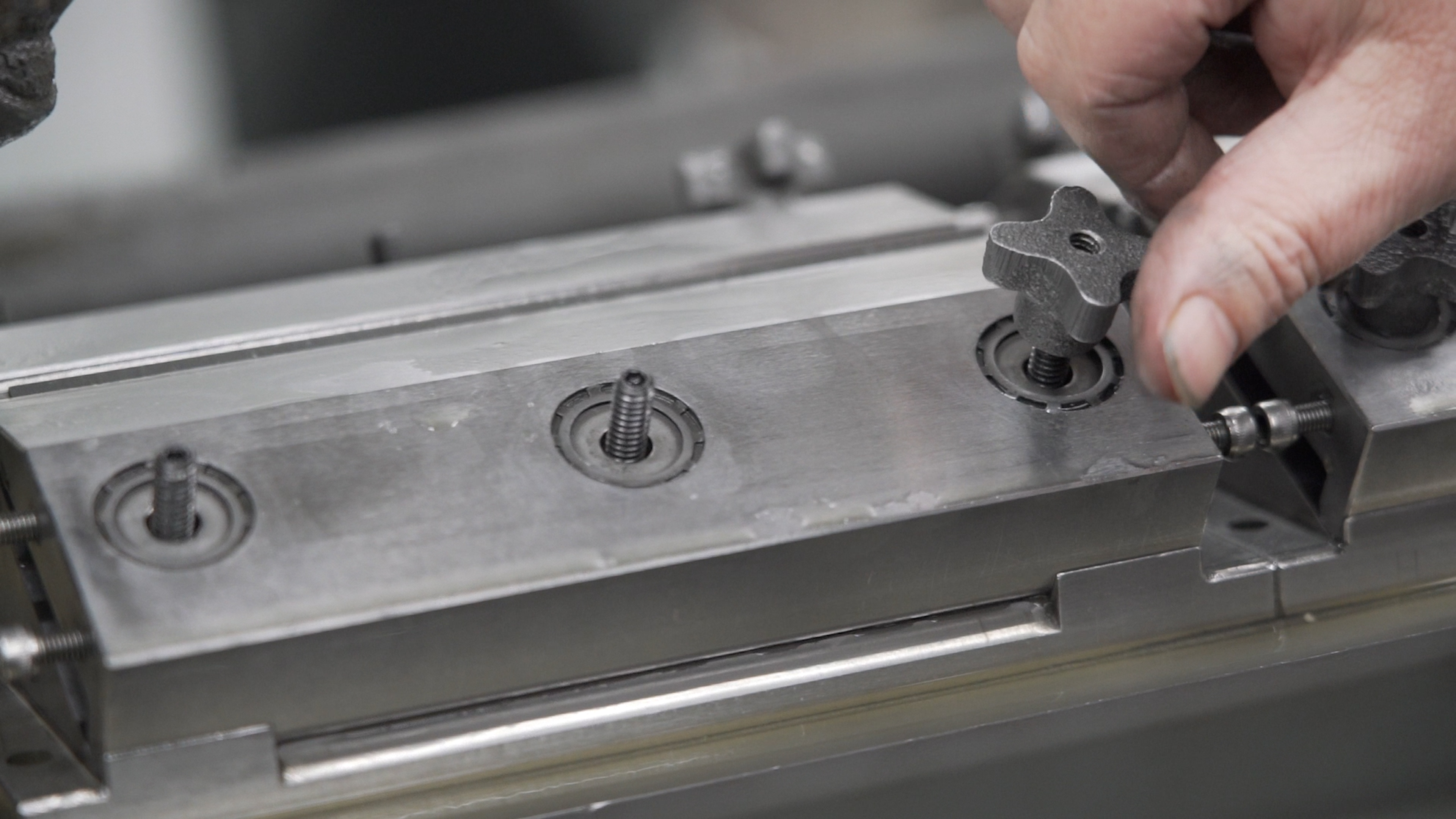
Why Your Job Shop Isn’t Productive (and What to do About it)
Although productivity is an important metric to keep in mind, it can be difficult to measure. Traditionally, many enterprises measure productivity through a variety of KPI’s centered on floor operations. On-time delivery, production schedule attainment, throughput, capacity utilization, yield, changeover times, and many others come to mind. These serve leadership well in determining how efficient and effective a shop floor is operating. However, these days performance carries a new element - one we consider above all most important: the human element.
As important as it is to track performance in measurable ways, it’s not all that uncommon to forget that there is immeasurable power in motivating and supporting the needs of your workforce. That can take the form of autonomy, respect, or even adapting to individual skills or job roles. But many enterprises struggle with antiquated software or pen-and-paper methods that have their shop floor battling to get through the daily minutia.
This leaves little room for operators to get to working on the company: expanding their skillset, acquiring new levels of career fulfillment, obtaining on-the-job training, or even just meeting (or exceeding) daily operational needs. In these new times, it’s not just about what gets done today: It’s about the pride of the job and the opportunity of tomorrow.
How to Build Back Worker Pride
At StartProto, we’ve put together our top three pain points that prevent workers from receiving the support they need and affect productivity. Though areas of concern now, these three main issues will continue to gain momentum as industry trends evolve over the next decade. By addressing them sooner than later, you’re not only supporting your operational workforce, but it can also equate to significant improvements in overall performance and productivity.
Moreover, you’re paving the way for the next generation of workers. In a recent survey over the jobs opportunities in manufacturing industry, 37% of millennials see manufacturing as a high-tech career. With this in mind, millennial workers are bringing with them high-tech skills necessary to support the evolution of the industry. As enterprises work to attract new talent, they’ll need to adapt recruitment techniques and practices that reflect the values of their next wave of skilled laborers.
1. You’re using ‘Legacy Software’
What is legacy software? Despite its benign-sounding name, Legacy Software translates to exceedingly outdated and obsolete technology that is impacting how efficiently your organization operates. For example, if you’re still tracking procedures through spreadsheets or antiquated manufacturing ERP software, you’re likely falling victim to Legacy Software.
Despite their original high value, these software solutions now require a significant amount of staffing effort to update and maintain. In some cases, organizations can take as long as 30 days to reconcile their reports. But these days, a variety of automated software solutions can cut out many of these repetitive tasks and cut time spent down by 60% or more.
2. Your operations run on tethered software on an in-house system
In this modern era, ensuring that your system is always up to date and accessible at the place of work is a necessity - especially if you’re clocking your competitors. With the prevalence of cloud based solutions, there is no reason to stick to stationary workstations that are out of the way or paper-reliant systems that don’t update in real-time. Fortunately, a variety of modern software solutions offer live tracking and real-time analytics - one of the foundational components of the StartProto system
3. You’re not utilizing ‘Self Determination Theory’ among your workers
It’s time for a little lesson in psychology.
If you’re looking to bring your advanced manufacturing enterprise to the 21st century, odds are you’re ready to incorporate an ‘operator-centric approach’ to bring back value and job pride to your workforce. This is where understanding Dr. Edward Deci’s Self Determination Theory comes in handy - especially if you’re looking to update your technology and integrate genuinely enjoyable software.
Dr. Deci noted that engaging employees and offering them input and feedback on processes improved their happiness and productivity, even when new protocols were introduced. This can be presented as greater autonomy with access to more freedom and control over their individual processes.
This has even been evidenced within the jobs in manufacturing industry, such as this study that determined workers who felt valued were more than four times as likely to report high levels of work engagement. We’ve also seen this play out first hand in our own customer case studies.
This exemplifies why StartProto embraces an operator-centric approach to our services. By working with both leadership and the floor, we can help utilize the skills and knowledge of both levels to improve productivity and cut back on stressful, remedial tasks.
But more than anything, giving your workers a voice can build a sustainable work culture that defies industry changes. The manufacturing world is evolving every day. And although Job Shops and advanced manufacturing enterprises alike will have to evolve too - there is no reason that your company’s core values and pride in a job well done can’t stand the test of time.
Conclusion
Unlock the potential of AI manufacturing
Blogs & Resources
Industry trends, manufacturing business tips, and more