The Advantage of StartProto’s Work-in-Progress Display System
Manufacturers often struggle with tracking work-in-progress (WIP) efficiently, leading to bottlenecks, production delays, and procurement issues. StartProto’s operation pills solve this by providing a real-time, visual way to monitor production progress at every stage.
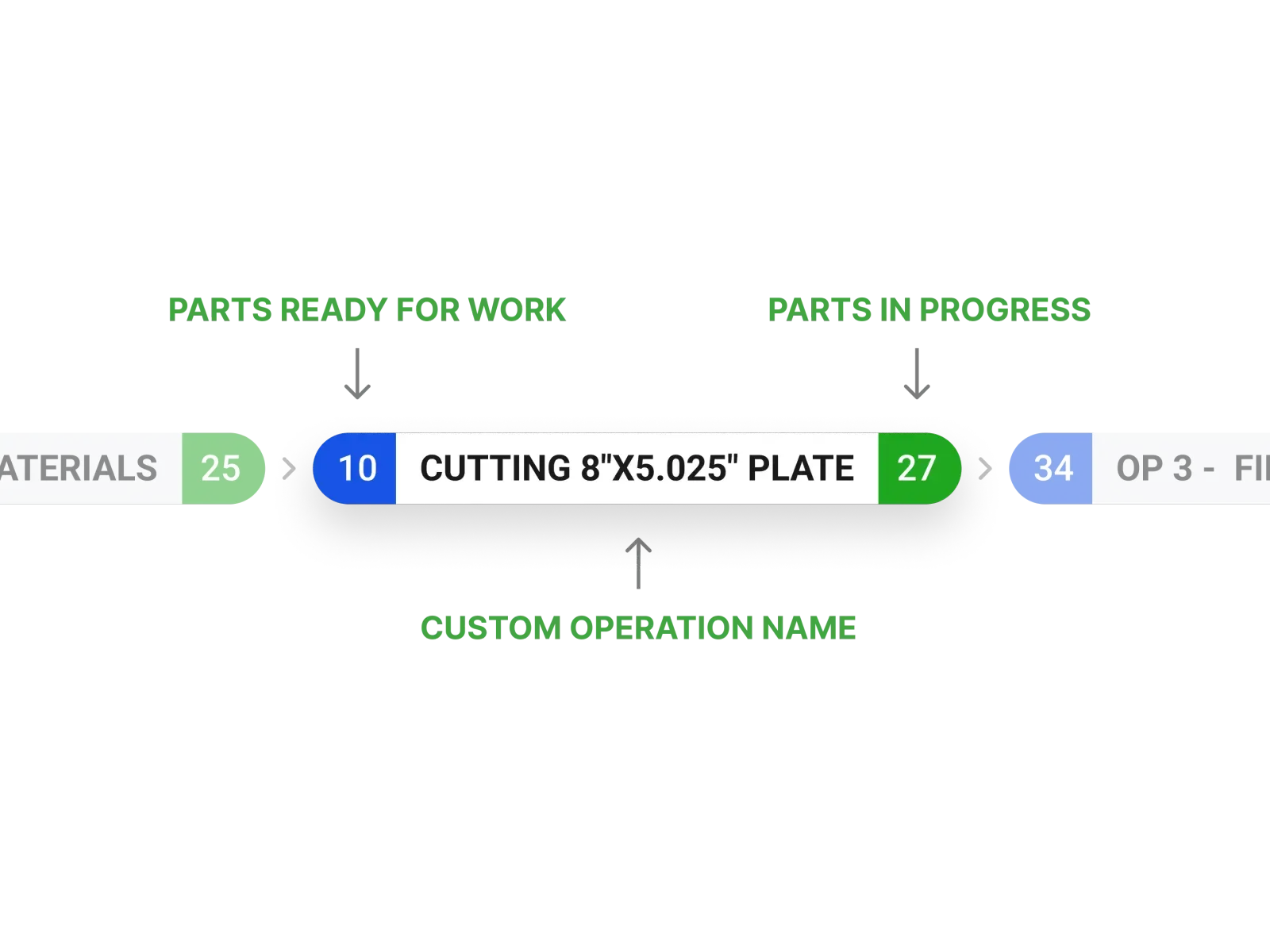
The Advantage of a Live Work-in-Progress System
Introduction
Manufacturers often have products moving through multiple steps on the shop floor at any given time. These unfinished products – known as work-in-progress (WIP) – can be challenging to track. Yet effective WIP tracking is crucial for efficiency. The challenge many factories face is visualizing WIP in real time. Without a clear view of how many parts are at each stage of production, managers struggle to make quick decisions, and delays or shortages can go unnoticed until it's too late. This is where StartProto’s innovative WIP display system comes into play, offering a visual solution to track parts in progress effectively.
What Are Operation Pills?
StartProto’s Work-in-Progress display revolves around operation pills – a simple, powerful visual tool for tracking production status. Operation pills are small, color-coded indicators in the software’s interface that represent the state of parts at each operation or workstation. They track two key numbers for each operation: how many parts are ready for work (i.e. completed at the previous step and waiting to be processed) and how many parts are active (currently being worked on in that operation). The core idea is that these pills always display counts in terms of completed parts. In other words, no matter which step of the process you’re looking at, the number shown reflects how many finished units those in-progress pieces equate to when completed. This approach gives everyone a consistent, easy-to-understand metric for progress.
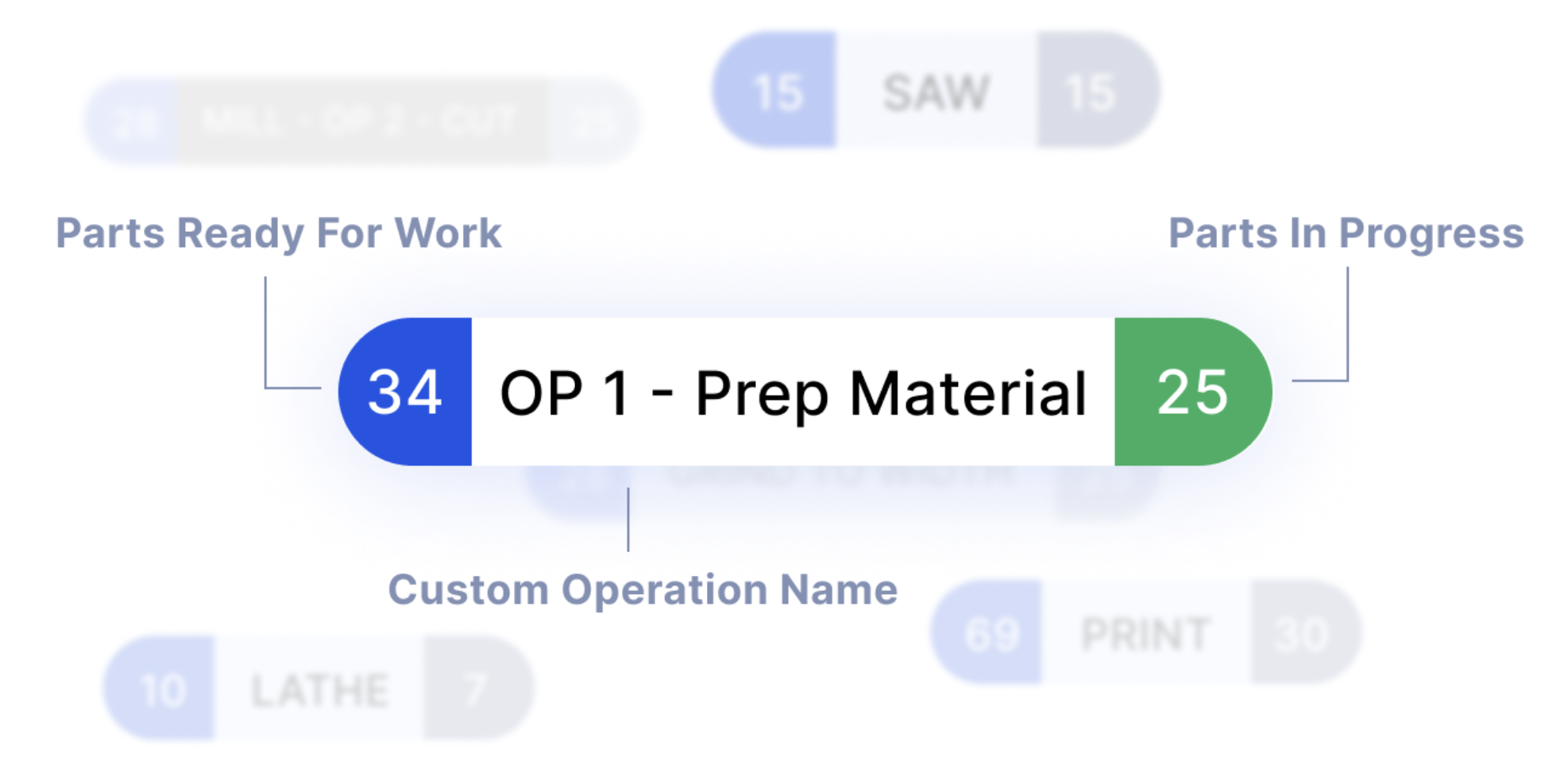
StartProto’s WIP BOM uses visual “operation pills” (highlighted number badges) to instantly show the status of parts at each production step. In the screenshot, each pill indicates the count of parts ready for the operation and the count active in that operation. Crucially, these numbers are shown in terms of fully completed units of product. This means managers and workers can immediately gauge how many final products are in progress at each workstation, eliminating guesswork that often comes with tracking partial assemblies or subcomponents.
The key benefit of operation pills is this consistent measure of completed parts. Unlike a generic WIP list that might show only raw piece counts at a station, StartProto’s pills automatically translate everything into “completed product” terms. If an operation is part of a larger assembly, the pill takes into account all required components. This way, a pill showing “5” at an assembly step truly means five finished products can be completed with the parts on hand. By always anchoring the numbers to completed units, StartProto ensures that every stakeholder interprets WIP status the same way – with a focus on final output.
How StartProto’s System Simplifies WIP Tracking
Traditional WIP tracking often involves manual counts or complex spreadsheets to figure out how far along each job is. StartProto’s system simplifies this by back-calculating completed parts from available stock at every stage. In practice, the software looks at all the materials and subassemblies available and computes how many finished goods they represent. This back-calculation is extremely useful for both straightforward fabrication operations and more complex assembly processes.
For example, a sheet metal manufacturer can use the system to see how many final parts are ready based on the current stock of cut pieces. If 50 metal blanks have been cut and are waiting at the bending station, the operation pill for bending might show “50 ready,” indicating those 50 pieces can be bent into completed parts. Managers no longer have to mentally convert work-in-progress into finished goods – the system does it automatically, updating the count as more pieces get cut or if any are scrapped before bending.
StartProto’s WIP display also shines in assembly operations by dynamically calculating how many products can be completed with on-hand components. In this example, a motor mount assembly requires 4 screws per unit. If there are 28 screws currently available, the system’s operation pill will show 7 assemblies can be completed (since 28 screws ÷ 4 per assembly = 7 full units). The screenshot illustrates how the operation pill for the assembly reflects the number of finished assemblies possible given the available screws and other parts. This real-time calculation means that at any moment, a supervisor knows exactly how many final assemblies can be built with the parts in stock. Moreover, StartProto tracks WIP at exact locations, so if any component or subassembly is scrapped or used elsewhere, the available count adjusts instantly. For instance, if a part is scrapped at an earlier station, the pills downstream immediately decrease their counts to reflect that loss. This high level of precision in tracking ensures that the numbers shown are always accurate and up-to-date, giving teams a trustworthy view of production status.
Why This System is So Effective
One reason StartProto’s WIP display is so effective is that these operation pills are propagated throughout the user interface, providing real-time visibility wherever you look. Whether you’re on the shop floor kiosk, a manager’s dashboard, or a procurement planning screen, the same live WIP information is displayed consistently. Everyone – from manufacturing managers to machine operators to procurement teams – sees a unified, current picture of production. This real-time propagation of data leads to smarter and faster decisions across the organization.
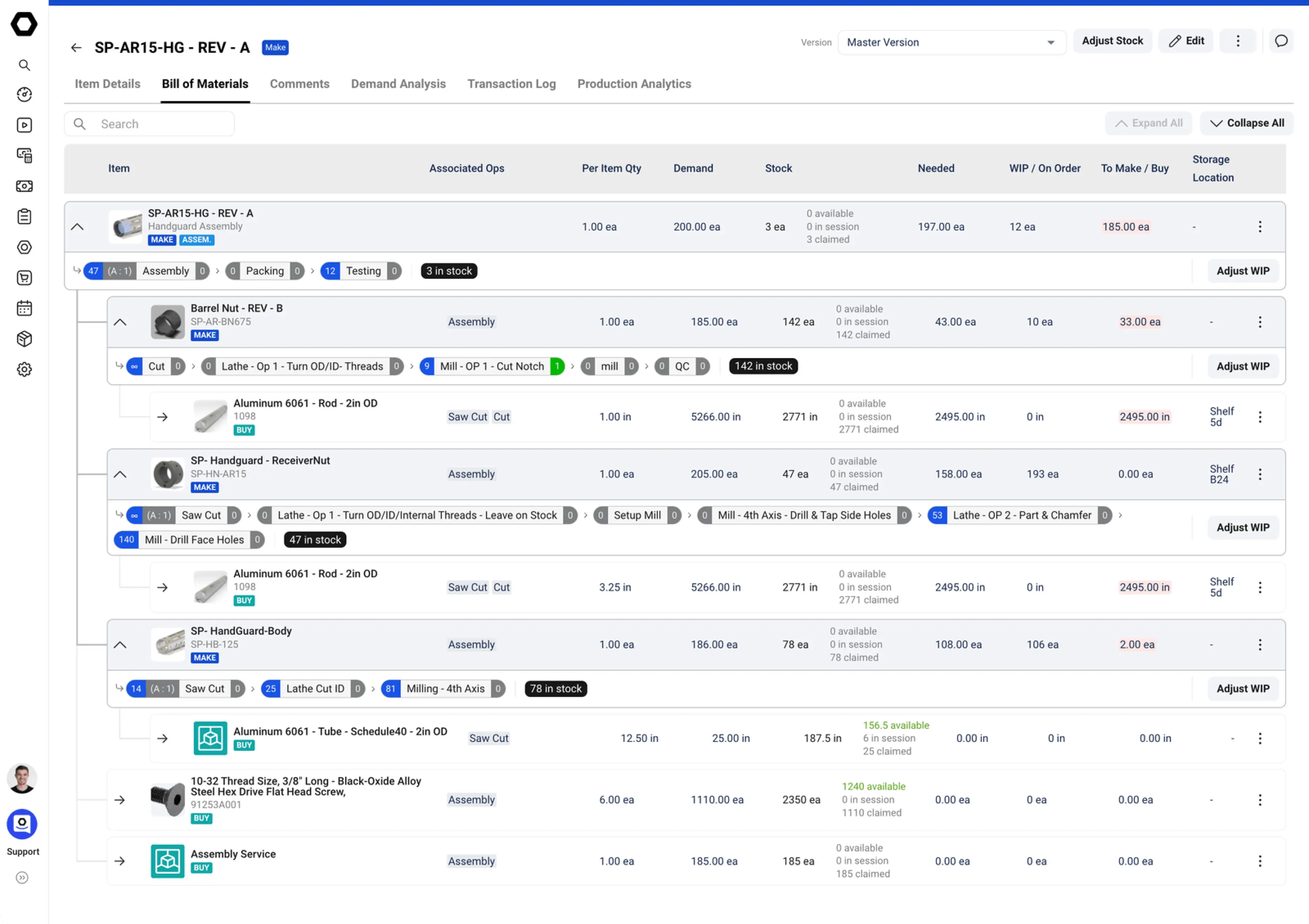
Consider the impact on different roles in a manufacturing company:
- Manufacturing Managers: Managers gain a high-level overview of all work in progress without having to call meetings or walk the floor to gather updates. They can identify bottlenecks at a glance if, say, one operation’s pill shows zero ready parts (meaning an upstream process is causing a holdup) or a large number of active parts (indicating a pile-up at that station). With this insight, managers can proactively reallocate resources or adjust schedules to keep production flowing smoothly. The clear visibility into how many finished units are moving through each stage also helps in more accurate forecasting and capacity planning, boosting overall operational efficiency.
- Shop Floor Operators: For operators and shop floor workers, the operation pills take the guesswork out of “what’s next.” They no longer need to wait for someone to tell them when more parts are coming down the line – they can see it in the UI. For instance, an operator at a milling machine can glance at the screen and see that 5 parts are active at the previous cutting station and about to be completed. This knowledge prevents unnecessary downtime or unnecessary setup teardowns. If the operator knows more parts are about to be ready, they might choose to keep the machine setup as is, rather than tearing it down and setting up for another job. In short, real-time WIP visibility helps operators sequence their work more efficiently, reducing idle time and extra labor.
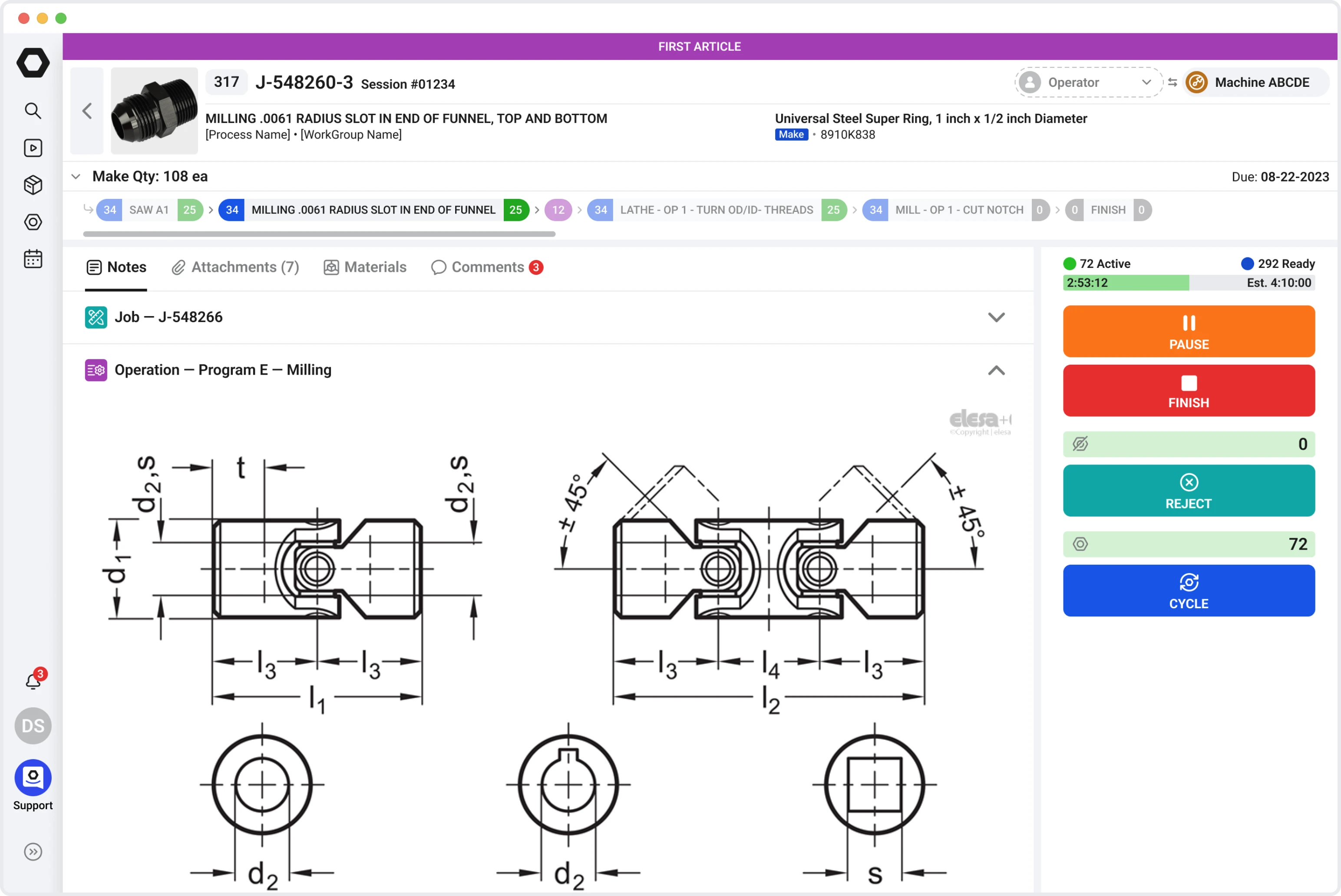
- Procurement Teams: Procurement and purchasing managers benefit from WIP visibility by making smarter inventory decisions. The operation pills offer early warning signals for component needs. For example, if an assembly operation’s pill is low because it’s waiting on screws or raw material, the procurement team will see that demand even before a formal alert might be triggered. They can take action to order or expedite the needed parts to prevent a stall in production. Conversely, if WIP indicators show that a certain job is nearly completed (or that some parts were scrapped and output will be lower), procurement can adjust orders for materials or inform suppliers and customers of changes. By having a finger on the pulse of WIP, purchasing can time material orders more precisely, optimize inventory levels, and avoid both shortages and excess stock. This leads to cost savings and ensures that production has the right parts at the right time.
Overall, the real-time WIP pills unify the entire team around a single source of truth for work-in-progress. Communication is improved because everyone is seeing the same status regarding how many parts are done, in process, or waiting at each step. The shop floor operates more cohesively with fewer surprises, and both managers and procurement can anticipate issues and opportunities rather than just reacting.
Conclusion
The impact of this WIP visualization is strong: jobs move through the shop quickly, setups and changeovers are optimized, and materials are procured just in time to keep the flow going. Manufacturing organizations that implement such a solution can expect less downtime, better use of resources, and more confidence in their production data. In summary, StartProto’s WIP display system doesn’t just track work-in-progress – it makes WIP work for you, by turning data into actionable, visual information. It’s a call to action for any manufacturer still relying on spreadsheets or gut feel to track WIP: invest in a modern, real-time tracking solution and watch your operational efficiency soar. Embracing tools like StartProto’s WIP display is a step toward smarter manufacturing and staying competitive in an industry where every part counts.
Unlock the potential of AI manufacturing
Blogs & Resources
Industry trends, manufacturing business tips, and more