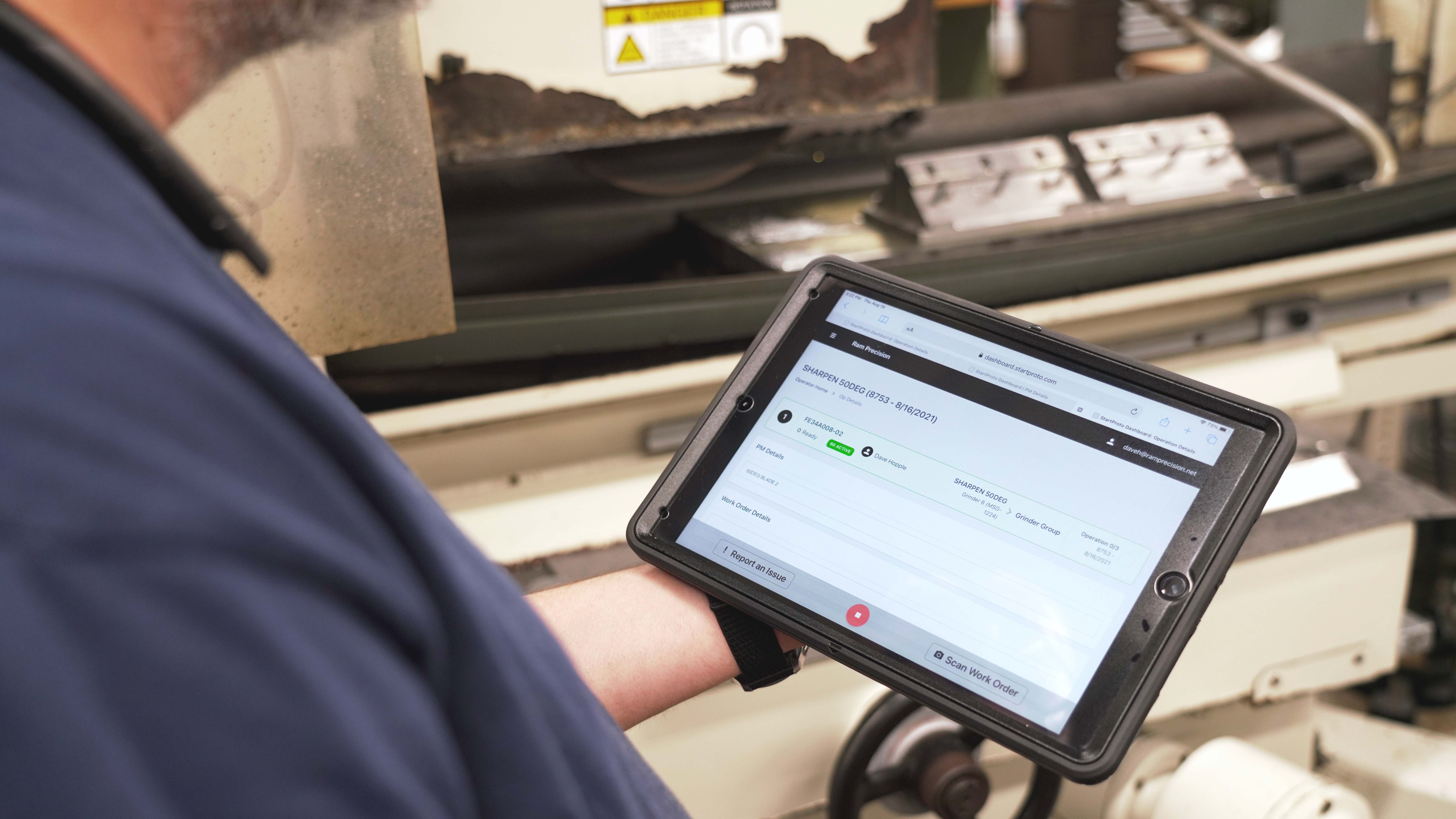
The 2017 Tax Cuts and Jobs Act (TCJA) significantly bolstered the manufacturing sector, leading to record job creation and wage growth. However, as highlighted in the National Association of Manufacturers' "What's at Stake: Tax Compendium," several key provisions are set to expire at the end of 2025, posing potential challenges for manufacturers.
Key Tax Provisions at Risk
- Pass-Through Deduction: Over 96% of U.S. businesses are organized as pass-through entities, paying taxes at individual income tax rates. The TCJA introduced a 20% deduction for these businesses, enabling them to reinvest in growth and job creation. This deduction is slated to expire at the end of 2025, which could lead to increased tax burdens for small and medium-sized manufacturers.
- Corporate Tax Rate: The TCJA reduced the corporate tax rate from 35% to 21%, enhancing the global competitiveness of U.S. manufacturers. While this rate is not scheduled to expire, proposals have been made to raise it to 28%, potentially diminishing the advantages gained from the initial reduction.
- Research and Development (R&D) Expensing: The TCJA allowed for full expensing of R&D investments, fostering innovation within the manufacturing sector. Without legislative action, this provision will phase out, making R&D activities more costly and potentially hindering technological advancements.
How MRP Technology Solutions Can Help
Given the looming expiration of these tax benefits, manufacturers must find ways to maintain profitability and efficiency. Material Requirements Planning (MRP) technology can provide crucial support:
- Cost Optimization: MRP systems assist in managing inventory levels, ensuring that materials are available for production while minimizing excess stock. This balance helps reduce holding costs and waste, leading to significant cost savings.
- Enhanced Production Planning: By analyzing production schedules and material availability, MRP software enables manufacturers to plan efficiently, reducing downtime and improving workflow. This efficiency is vital in offsetting potential increased tax liabilities.
- Improved Decision-Making: MRP systems provide real-time data on inventory, production status, and demand forecasts, empowering manufacturers to make informed decisions quickly. This agility is crucial in adapting to changing tax landscapes and market conditions.
- Resource Allocation: Efficiently managing resources such as labor and machinery ensures optimal utilization, reducing operational costs. MRP software aids in scheduling and workload management, contributing to cost efficiency.
- Scalability and Flexibility: Modern MRP solutions are scalable, allowing manufacturers to adjust operations seamlessly as business needs evolve, which is essential in responding to potential tax changes.
Conclusion
By leveraging MRP software, manufacturers can enhance operational efficiency, reduce costs, and better position themselves to navigate the uncertainties associated with the expiration of TCJA provisions. Proactive investment in such systems can mitigate the impact of potential tax increases and maintain competitiveness in the evolving economic landscape.
Try StartProto for free today and future-proof your operation through automation and intelligence.
Unlock the potential of AI manufacturing
Blogs & Resources
Industry trends, manufacturing business tips, and more