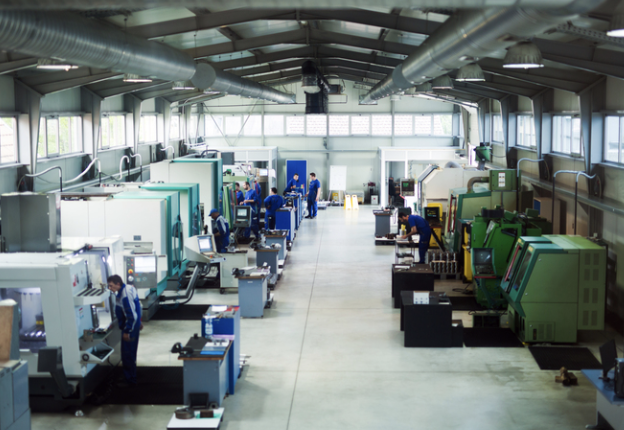
With a variety of different software tools geared towards job shops and manufacturing facilities, it can be easy to get confused with all the options. MRP and MES acronyms get passed around as necessary tools in the manufacturing process, but what do they really do? Which one is better? Given the different options in the marketplace, how do manufacturing shops determine which one to optimize their manufacturing processes?
MRP software (Material Requirements Planning) is primarily focused on the planning aspect, including material requirements, inventory management, and procurement scheduling to ensure that materials are available for production at the right time. It deals with the "what" and "when" questions of manufacturing. MES, (Manufacturing Execution Planning) on the other hand, focuses on the execution phase of manufacturing. It controls and monitors the transformation of materials into finished goods, managing the "how" aspects of production, such as process control, real-time data collection, and shop floor operations.
MES Software- The What and When of Manufacturing
MES systems primarily focus on the shop floor, offering real-time monitoring, control, and documentation of manufacturing processes from raw materials to finished goods. It enables production tracking, resource management, and quality control- optimizing schedules, reducing downtime, and ensuring efficient resource allocation.
Various job shops, production floors and manufacturing shops benefit significantly from MES systems due to their ability to improve efficiency, reduce waste, and enhance product quality.
MES Systems Key Functions and Benefits
When evaluating different MES systems, many teams look to help optimize the following:
Production tracking and resource management: Cloud based MES systems Track products, materials, and processes throughout the manufacturing lifecycle, optimizing production schedules and reducing downtime.
Real-time data collection and analysis: Provides insights into production performance, resource utilization, and quality metrics, facilitating informed decision-making and optimization of production processes.
MRP Software- The How of Manufacturing
In contrast, MRP software primarily focuses on inventory management, production planning, and scheduling. It calculates the materials and components needed for manufacturing, helping businesses maintain optimal inventory levels and timely procurement of materials. When evaluating different MRP systems, many job shop owners look to help optimize the following:
MRP Systems Key Functions and Benefits
Accurate Planning and Forecasting: MRP software systems help predict material requirements based on customer demand, ensuring manufacturers can meet production targets and schedules efficiently.
Reduced Lead Times and Costs: By streamlining the procurement and production processes, MRP software can reduce manufacturing lead times, minimize waste, and lower costs.
Improved Customer Satisfaction: With better inventory management and production planning, companies can offer shorter lead times, enhancing customer service.
Blending them together by using StartProto
A solution like StartProto, which integrates both MRP (Material Requirements Planning) and MES (Manufacturing Execution System) functionalities, offers a comprehensive suite of tools that address both the planning and execution phases of manufacturing. This integration brings several benefits to a manufacturing shop:
Streamlined Operations
Integrating MRP and MES functionalities into a single solution like StartProto simplifies the manufacturing process. It eliminates the need for separate systems to handle planning and execution, thereby reducing the complexity and potential for errors in data management. This combination ensures that the planning, scheduling, inventory control, and execution of manufacturing processes are seamlessly aligned, leading to more efficient operations on the job shop floor.
Enhanced Visibility and Control
By combining MRP and MES, shop owners can gain enhanced visibility into every aspect of the production process, from raw material procurement to final product delivery. This unified view allows for real-time tracking and management of resources, schedules, and shop floor activities, enabling better decision-making and control over the manufacturing process.
Improved Resource Optimization
The blending of an MRP and MES software system like StartProto helps optimize the use of resources, including materials, machinery, and labor. MRP components ensure that materials are available when needed, minimizing inventory costs and waste, while MES components optimize production schedules and labor allocation based on real-time data. This leads to improved efficiency and productivity, reducing lead times and costs.
Increased Flexibility and Responsiveness
A combined MRP and MES solution like StartProto allows manufacturing shops to be more flexible and responsive to changes in demand, production requirements, and unforeseen challenges. The system can quickly adjust production plans and schedules based on real-time data, enabling manufacturers to respond swiftly to customer demands, supply chain disruptions, or equipment failures, thereby minimizing downtime and maximizing output.
Data-Driven Decision Making
A solution that combines MRP and MES functionalities provides a healthy amount of data that can be analyzed to make informed decisions. This data-driven approach allows manufacturers to identify trends, inefficiencies, and opportunities for improvement, leading to continuous process optimization and innovation.
Conclusion
In the end, job shop owners need to consider solutions that provide them a combination of MES and MRP functionality. With StartProto, the tool not only simplifies and streamlines operations but also provides the tools necessary for manufacturers to optimize resources, enhance flexibility, improve product quality, and make data-driven decisions for greater profitability.
For those of you looking to start optimizing your manufacturing or job shop floor, give StartProto a try for free. Click here for a free entry-level license.
Unlock the potential of AI manufacturing
Blogs & Resources
Industry trends, manufacturing business tips, and more