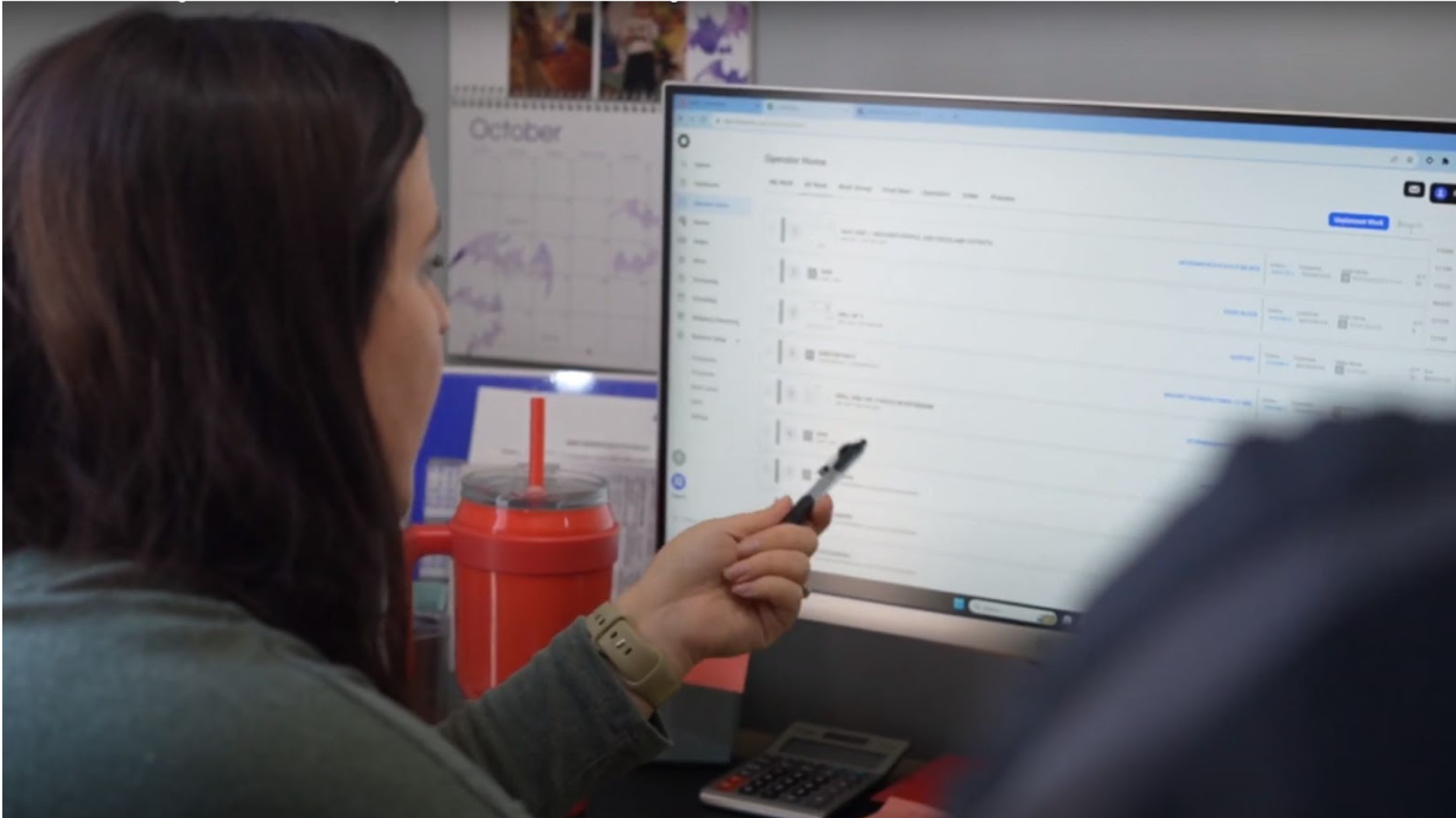
What Is Cloud Manufacturing?
Cloud manufacturing is the process of using digital manufacturing solutions, such as MES, MRP, and ERP software, through “the cloud.” In other words, you’re getting everything that already makes on-premise software great and moving it off of local servers and hard drives and onto the internet. When your system lives on the cloud, you can spend less time working with IT on installations, updates, and upgrades, and more time focusing on the success of your business.
Cloud-based ERP systems for manufacturing have become increasingly popular due to conveniences such as:
- Faster setup than on-premise software
- Ease-of-use across many devices
- Location-independent accessibility (in the back office, on the shop floor, and even in separate geographic locations)
- Automatic software support/updates from the service provider
With a manufacturing cloud in place, your business can unplug and collaborate with more ease than ever before.
Manufacturing Technology is Changing
Going paperless in your shop once meant an escape from familiar problems — stuffed file cabinets, limited instructions, lost records, illegible info, mismatched data on different forms — and the introduction of an entirely different, new set of problems.
The Old Way
Legacy on-premise ERP systems could often be highly demanding, in terms of time, budget, and training. Without an in-house IT team, any technical support problems could be a real headache. Software updates were time-consuming and hands-on, sometimes even requiring a costly purchase of a new version. The investment required for hardware, software, installations, security, and was significant.
Many of these systems also tried to do too much, acting as do-it-all sandboxes full of complex capabilities across all possible business functions that required hours of training, and very long implementation cycles — and precluded the use of separate, familiar solutions like Quickbooks, which remain popular for machine shop accounting.
The New Way
All of this is changing with modern, cloud-based manufacturing ERP systems. The industry is moving away from mammoth, singular systems that do everything, and turning instead to polished point solutions that are tied together very well. Strong API functions allow for smooth integrations and handoffs of data for specialized processes that each preferred software solution does best. These more agile, cloud-based ERP systems for manufacturing also eliminate the frustrations common to on-premise software.
Your team doesn’t need to deal with the upkeep of the software, technical support, cybersecurity, or repurchasing as new versions are released. The cloud software provider handles it all for you. From product modeling to quoting, work routing, inventory management, and schedule management, a targeted and convenient solution for your core machine shop production workflow keeps things moving in full alignment. No matter what step of production a job is on, relevant information is carried forward in a consistent, user-friendly manner. Machine operators can stay on the same page as production managers and the sales reps who handle RFQs.
Ideally, operators can pick up a tablet anywhere in the shop and scroll through detailed, step-by-step work instructions, complete with diagrams, photos, and design files. When work is complete, it’s easy for production managers to view the job’s status. Sales reps can view feedback from the shop floor to inform quotes on new work. Efficiency gains are a given with paperless manufacturing on the cloud.
How to Ensure Your Machine Shop is Successful
Amidst an uncertain economy and a changing tech landscape, shops must do everything they can to stay competitive. CEO Joey Jones of Aerotech Machining said to Modern Machine Shop that “In this business, technology moves so fast that if you’re not changing you’re falling behind.”
Keeping current with a cloud-based ERP for manufacturing can give you a vital edge, but it’s just the tool. It takes the right mindset and priorities to ensure success.
Everything comes back to profitability. Revenue does matter — shops need to keep cashflow coming and make payroll on time — but sustainable margins on good, profitable work are more important. Here are a few tips to help you stay on the right track.
- Bring in the Right Kind of Work
No shop can function without bringing in work. However, not all work is good work. You might spend time on activities such as attending trade shows to collect leads, but make sure you’re separating good work opportunities from bad ones, and prioritizing the right kinds of jobs.
Cloud manufacturing solutions are excellent at helping you to examine trends in the jobs that are coming in, how long it takes to complete them, and how they’ve affected your bottom line. Unified, easily accessible insights and visibility into the overall production process can be the key to identifying the kinds of work your shop should prioritize in future opportunities.
- Optimize Work Definition, Planning, and Execution
Accurate, detailed and consistent work instructions prevent costly errors and delays. This is where paper-based machine shops tend to feel the most pain. Post-it notes, travel packets and legacy knowledge can create bottlenecks and delays. Without a shared electronic system for work definition and routing, document storage, and task scheduling, it’s hard to keep production moving in an efficient manner. see the forest for the trees. A paperless, cloud-based process can help manufacturers achieve 15% greater daily production output due to fewer manual steps, less human error, and more efficient information flow.
Cloud manufacturing systems eliminate bottlenecks throughout the production process. You can stay a step ahead in your material purchasing with greater visibility into overall needs, inventory on hand, and timing for reorders. More cohesive inventory management helps you to achieve more competitive lead times and avoid idle machines sitting around waiting for materials.
- Prioritize Communication, Inside and Out
Inefficient legacy ERP systems, Excel spreadsheets, and paper-based documentation processes are the bane of efficient, accurate, timely communication in the shop. With cloud manufacturing software, you can break down information silos and ensure the whole team stays connected with a single, shared repository of information.
Shops with strong internal communication improve quotes, results, and profits. It’s best to have a system in place that empowers front-line operators to share feedback and comments in a bottom-up communication model. When relevant and timely information from the shop floor flows up the chain to leadership and job quoters, you’re helping your decision-makers to make more informed decisions.
External communications also deserve attention. Repeat customers keep coming back to use your shop because their customer relations experience has been smooth and positive. Conscientious communication — automatic shipment emails, touching base about lead times, updates on job status, and the like — will endear you to customers and make your shop more human (i.e. not merely a transactional vendor). Cloud ERP systems can facilitate automatic updates and also help you to more quickly and easily check on statuses and timelines to share with your customers.
- Analyze to Continuously Improve
Between challenges like labor and skill shortages, supply chain disruptions, and an unstable economy, machine shops have their work cut out for them. It’s important to make smart, data-driven decisions to stay competitive and keep your profitability sustainable.
Research from Accenture has shown that cloud-based analytics can dramatically improve production performance for manufacturers like machine shops, including:
- Boosting asset utilization by 5-15%
- Increasing yield by 15-25%
- Improving worker productivity by 30-40%
- Reducing inventory holding costs by 20-30%
- Accelerating time to market by 30-50%
The rich data collected within a cloud manufacturing ERP can fuel vital internal analytics efforts with real-time insights, a central repository for all documentation, and simple data reporting. Indeed, your manufacturing cloud also frees up the time and resources for this sort of analysis. Rather than spending those resources on pushing paper and manual schedule-building, you can focus that energy towards helping your business to continuously improve and grow.
Conclusion
Optimize Your Machine Shop With StartProto
StartProto is the purpose-built cloud manufacturing platform that makes it easy for machine shops to monitor and improve every stage of production. Whether you’re going paperless for the first time or need a replacement for legacy systems, StartProto has the tools to help. Our software seamlessly connects your shop floor operations, real-time data, and inventory management on a platform that grows with your business.
Did you know that you can start using Startproto’s platform for free? When you’re ready, get in touch with our team to book a demonstration or sign up for the free version of our software and get started with StartProto for free.
Unlock the potential of AI manufacturing
Blogs & Resources
Industry trends, manufacturing business tips, and more