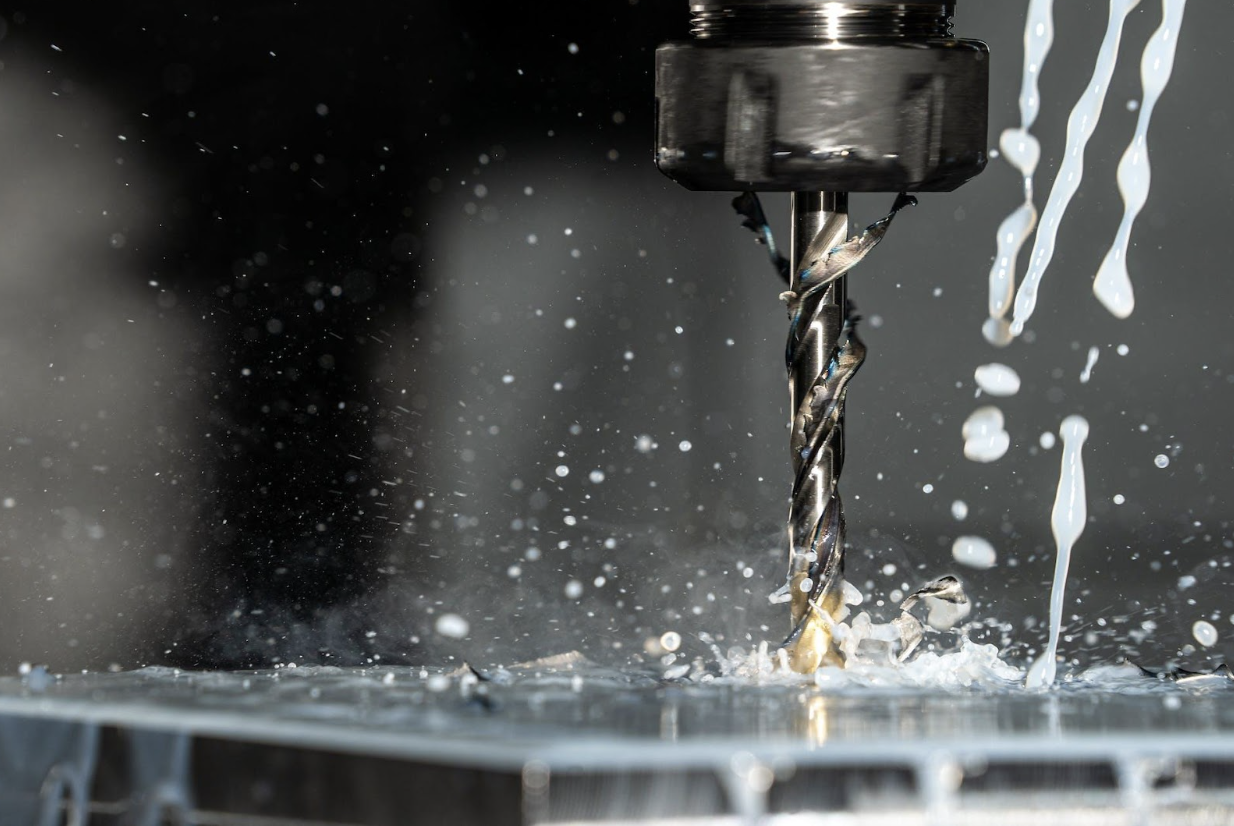
Many shops struggle to optimize their material purchasing process for incoming work. Unfortunately, this can lead to bottlenecks and delays on the shop floor. A cloud-based bill of materials software for your purchasing team may be the answer you’ve been looking for.
After all, a seamless workflow — from the initial RFQ to the shipment of a completed product — is essential to the profitability of any machine shop or contract manufacturer. Cloud manufacturing platforms bridge the gaps between each step.
The right manufacturing software system will not only eliminate the guesswork, but boost productivity and help to improve lead times (ultimately earning you more work).
Define → Plan → Execute: How the Bill of Materials Impacts Your Workflow
Once you have a pipeline of lucrative work coming in from the sales team, the next step is to build an efficient execution process that handles everything from material purchasing to inventory management, job routing, and document storage.
It’s crucial to create a smooth handoff to and from the purchasing team, who are something of a keystone in the middle of the shop’s workflow:
- Defining: This first step includes item definition and routing of work. The client, sales team, and engineers will work together to define parts for upcoming jobs, materials they’ll require, and step-by-step instructions for production.
- Planning: Here’s your purchasing team. They need to take the Bill of Operations (BOO) and Bill of Materials (BOM) and determine what materials to buy, how much you need, what’s already on hand in your inventory (if you carry any), and whether you have enough stock on hand for upcoming work to start (and finish) on time. Then they’ve got to place orders and keep track of them.
- Execution: At this stage, tasks must be assigned and scheduled in clear, sequential steps for operators on the shop floor. However, operators won’t be able to get started until the right manufacturing materials are on hand, and if any rework or changes are required, they’ll need to communicate with the purchasing team to let them know which additional materials are needed.
It helps to keep the wheels greased, so to speak, if you can establish consistent, standard operating procedures for item definition, work routing, and creating of the Bill of Materials. A clear manufacturing BOM handoff from work definition to the purchasing team will help to ensure timely purchases and faster work.
StartProto Solves Common Bill of Materials Challenges
Optimizing orders can require some degree of juggling. The purchasing manager has to balance lead times, unit sizes, and lot sizes, while maintaining an open feedback loop with the engineers and the shop floor.
StartProto is the cloud-based Bill of Materials software that keeps all teams aligned in a single system — a single “source of truth” — from BOM to shipping for consistent performance.
- Visibility Into Overall Material Needs, All In One Place
A cohesive cloud-based BOM for a job is more than a convenience at the individual job level. It also makes it possible to aggregate all current demand for materials into one place, across all jobs, so that you can automatically calculate the total materials needed, their cost, and how trends change over time.
Insights like these can help you to move from blind bulk ordering to coordinated and scheduled deliveries from vendors, especially if your shop has any predictable repeat work. With a consistent schedule for material purchasing, you can move towards smaller overall invoice quantities that will line up better with your production schedule and current cash flow levels.
On the other hand, you can also more easily achieve economies of scale on materials by buying in larger quantities where and when it makes sense. Either way, StartProto will generate a list of precisely what you need to buy with every incoming job. This makes it simple for the purchasing team to have the correct materials in place, early, and ensure they’re not preventing any urgent work from getting started.
- Bird’s Eye View of All Materials Currently On Hand
If your job shop carries any inventory for commonly requested or repeat work, accurate inventory tracking will be crucial for shop efficiency and avoiding delays. Manual tracking takes time and leaves room for error. Automation tools in a comprehensive cloud-based MRP software can transform time-consuming daily or weekly inventory cataloging into an instantaneous process.
On the front end, it’s important to invest sufficient time into item definition in your system. From there, viewing or updating inventory levels is as easy as a few clicks, from anywhere in the shop, and levels can be automatically updated when jobs are completed (and on-hand materials were used up).
- Quicker, Data-Driven Decisions on Reordering
Shops that rely on high-volume, low-mix work will often have ready-to-go inventory on hand for fast production. However, even low-volume, high-mix shops that focus on prototypes or other specialized projects can benefit from immediate insights into material order statuses for quick ordering. Precise inventory tracking with cloud MRP software is essential for fast decision-making on reorders and rapid curation of purchase lists for rush jobs or repeat customers.
- No More Bottlenecks & Idle Machines
The worst case scenario for any job shop is for expensive machines to sit, unused, while work is waiting to be done. Unfortunately, this is a common issue encountered by shops that haven’t optimized their material management systems. Oversights, delayed material arrivals, and reduced operational efficiency are a direct consequence of poor material planning.
Advance planning and timely material procurement with efficient, automated software keeps your machines operating at maximum uptime and eliminates material bottlenecks. Machines and operators can only make the most of their time if they have the materials they need, ready to go.
- Paperless Productivity Improvements
If your material purchasing process intersects with an in-shop paper trail, you’re leaving money on the table due to lost efficiency. A paperless process can lead to a 15% greater daily production output, as observed in a case study reported by CHEManager International in 2022.
Transitioning to a shared electronic manufacturing MRP streamlines production, largely due to fewer manual steps, fewer errors, and a more efficient flow of information.
- Easy Access to the BOM From the Shop Floor
Cloud-based bill of materials software allows your purchasing manager to benefit from a continuous feedback loop with engineers and operators on the shop floor — all with fewer walk-in interruptions during the day.
StartProto provides operators with seamless access to premade lists of the day's work, complete with step-by-step work instructions, diagrams, drawings, setup sheets, 3D models, and the full manufacturing bill of materials. Clear documentation, accessible right from their list of work, eliminates all back-and-forth with production and purchasing managers and makes the most of everyone’s time.
Try StartProto Today to Optimize Purchasing and Materials Management
Our cloud-based MES, MRP, and Bill of Materials software is purpose-built to eliminate bottlenecks and enhance shop efficiency. By streamlining material purchases and simplifying the job routing process, your team can realize throughput improvements, and, in the end, more client satisfaction and work opportunities. Stay ahead of the curve and lead your shop towards success by giving StartProto a try today.
Conclusion
Move your manufacturing to the cloud
Blogs & Resources
Industry trends, manufacturing business tips, and more